FMCG (Fast Moving Consumer Goods)
CrateDB enhances FMCG operations by optimizing shopfloor efficiency through real-time equipment monitoring and workflow optimization. It ensures product quality with integrated quality control measures, reducing defects and waste. Additionally, CrateDB enhances compliance and traceability by enabling batch tracking, regulatory reporting, and swift recall capabilities.
Shopfloor Optimization
Real-time Equipment Monitoring: CrateDB enables FMCG companies to monitor the performance of machinery and equipment on the shopfloor in real-time. By analyzing data on machine uptime, downtime, and performance metrics, manufacturers can identify inefficiencies, schedule preventive maintenance, and minimize production disruptions.
Workflow Optimization: CrateDB helps optimize workflows on the shopfloor by analyzing data on production processes, inventory levels, and employee productivity. By identifying bottlenecks and streamlining workflows, FMCG companies can increase throughput, reduce lead times, and improve overall efficiency in manufacturing operations.

Quality Control
Real-time Quality Monitoring: CrateDB facilitates real-time monitoring of quality parameters during the production process. By integrating with sensors and quality control systems, FMCG companies can continuously monitor product attributes such as size, weight, and color, ensuring consistency and compliance with quality standards.
Defect Detection and Analysis: CrateDB enables FMCG companies to analyze data on product defects and deviations from quality standards. By identifying patterns and trends in defect occurrence, manufacturers can implement corrective actions, improve production processes, and reduce waste caused by defective products.

Compliance and Traceability
Batch Tracking and Traceability: CrateDB enables FMCG companies to maintain detailed records of product batches, ingredients, and manufacturing processes. By storing this information in a centralized database, manufacturers can quickly trace products throughout the supply chain, ensuring compliance with regulations and facilitating efficient recalls if needed.
Regulatory Reporting and Auditing: CrateDB supports compliance with regulatory requirements by providing tools for generating reports and conducting audits. By analyzing data on production processes, quality control measures, and ingredient sourcing, FMCG companies can demonstrate adherence to industry standards and regulations, streamlining compliance efforts and reducing the risk of fines or penalties.

FMCG companies operate at an astonishing speed, producing hundreds of thousands of goods every hour. This rapid production rate emphasizes the need for real-time quality control measures. Delaying the identification of any production quality issues, even by a few minutes, can result in significant financial losses, not to mention the disposal of a substantial number of products and the immediate impact on the company’s reputation. By reading the two case studies below, discover how FMCG companies leverage CrateDB to power real-time analytics in high-volume data architectures.
Case Study #1: Rauch Group
The RAUCH Group occupies three strategic business fields. In addition to producing and selling fruit juices under the RAUCH brands, the company is also firmly established in the business-to-business area. Within this branch, the company RAUCH carries the role of a producer and sales company for international purchasers of fruit juice concentrates and half-finished products. The third field concerns commissioned fillings. As a service provider, RAUCH fills for other producers of beverages with the proper high-tech filling installation for cans, PET (plastic) and glass bottles.
Key objectives
- Real-time production dashboards and historical analytics shared across plants & lines to improve Overall Equipment Effectiveness (OEE).
Main technical challenges
- Complexity of records of both structured (ERP) and unstructured data (sensors).
- High speed ingest from multiple data sources & massive scaling requirements.
- Simple integration with existing systems, across continents (US & Europe)

120,000 |
cans per hour per line |
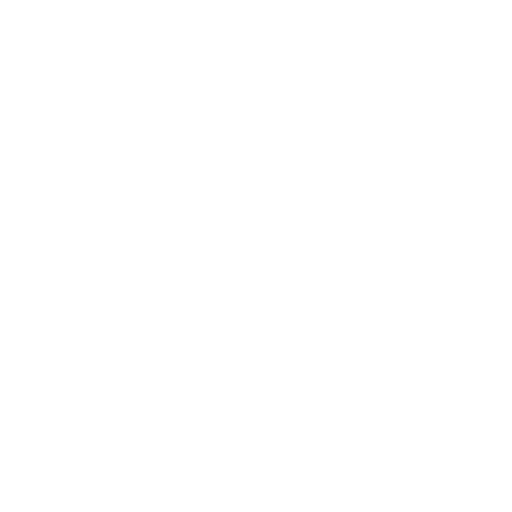
Case Study #2: ALPLA
ALPLA is a world leader in the area of packaging solutions, producing high-quality packaging for Coca-Cola, Unilever, and other brands in the food, drinks, cosmetics and cleaning industries. ALPLA employs 20,900 employees at 181 locations across 46 countries.
Key objectives
- Provide real-time dashboards to 1.000s of employees.
Main technical challenges
- Get quick insights into production data mix (ERP data/Sensor Data, Quality Data).
- Store large amounts and a variety of data (relational, JSON & timeseries data) for real-time access across 180 plants.
- Plan for simple growth when adding new lines and plants, fully integrate with existing systems.
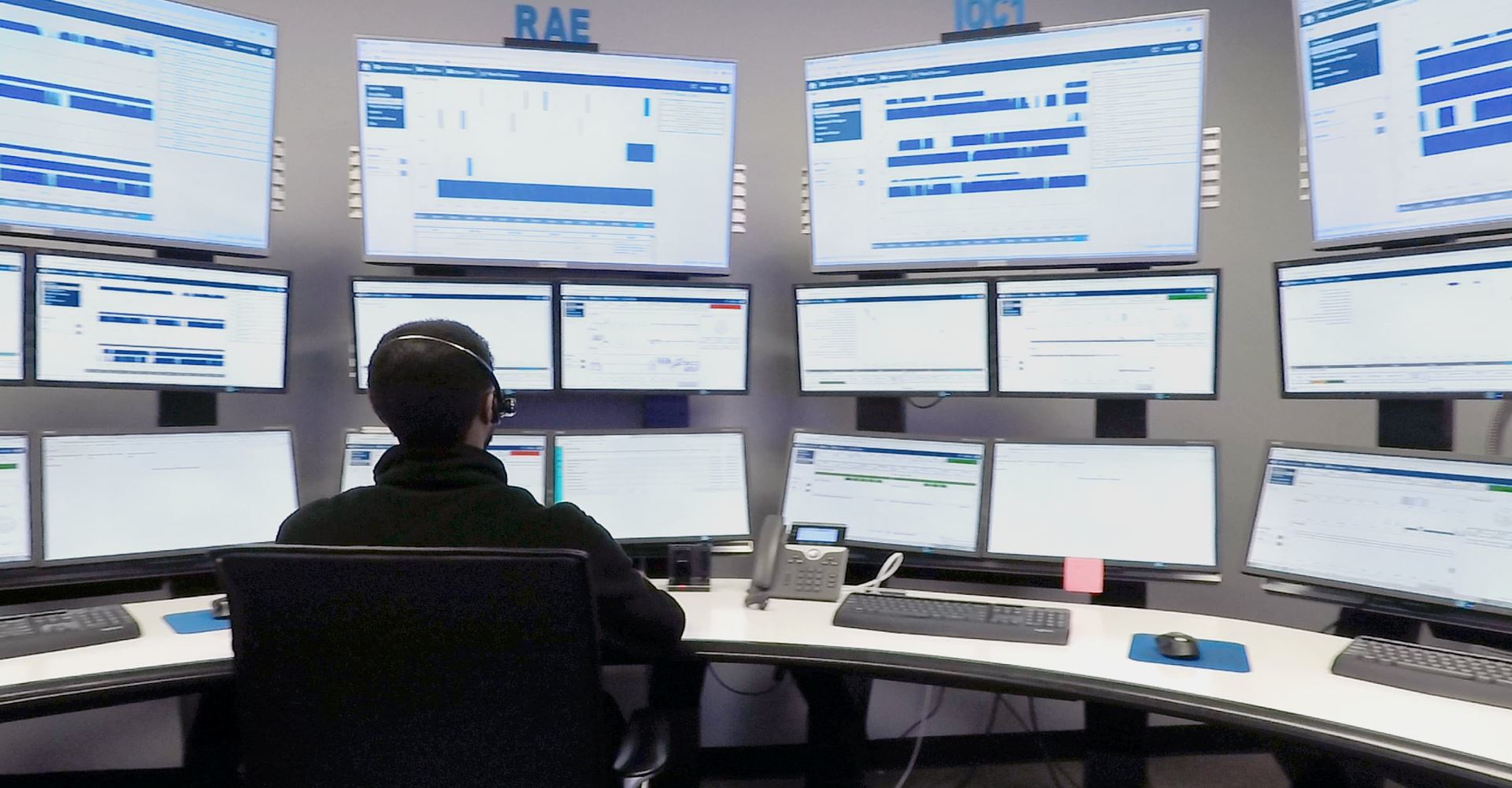
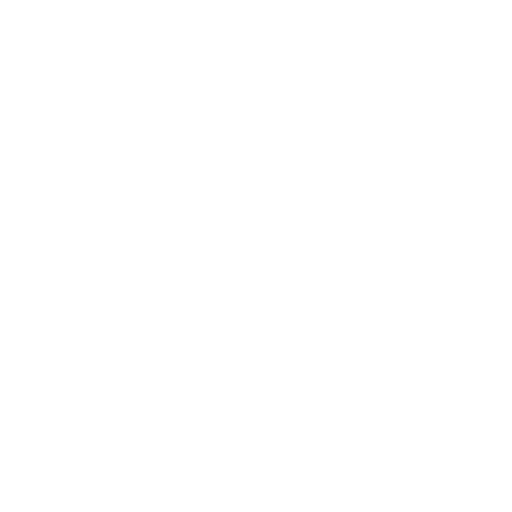