Data science in manufacturing . . . without the data scientists

Matt Chaban
Senior Editor, Google Cloud
Manufacturers are awash in data-- and the cloud is helping turn it into value
The economic swings of the pandemic, supply chain shortages, economic and political uncertainty, and climate change have all deepened a decades-long debate about manufacturing jobs. What are they? Who should do them? Does anyone want to do them? Why can’t we find enough people to do them? Will they ever come back?
According to the European Commission, the manufacturing sector lost about 750,000 jobs across the European Union between 2013 and 2019. In 2021, a team at Deloitte noted instability in the United States too, with over half a million factory jobs lost the previous year— despite a near-equal number of manufacturing openings remaining unfilled. And things have only gotten more challenging for plant managers since: research by the St. Louis branch of the Federal Reserve found as many as 900,000 manufacturing job openings at the end of 2021. Vacancies have hovered around that point to this day.
One particular issue is that as manufacturing has grown so much more advanced, the skills required to operate the highly automated, data-driven machinery have evolved too, exceeding the expertise of many traditional workers.
“These are not our grandfather’s, or even our father’s, generation of factories — even if they were established many years ago,” Simon Floyd, the director of manufacturing and transportation industries at Google Cloud, said in a recent interview. “There is an immense amount of data that is available to answer manufacturing’s most challenging questions.”
Artificial intelligence, advanced analytics, machine optimization, or predictive maintenance — none of this is possible without a solid data operation to build upon. And you need workers who can build upon that data, too.
“Data is the heart of everything manufacturers do,” said Charlie Sheridan, global technical director for manufacturing, automotive, and energy at Google Cloud. “If you don’t have a strong data foundation, you will struggle to build any value-add use cases, including AI-based optimizations. I think what’s happening today is that companies are starting to focus on the whole concept of the industrial data cloud.”
With that focus comes requirements for a workforce that can use data to its greatest advantage. This brings manufacturing engineers closer to data scientists on the skills chart. Data skills platform QuantHub estimated in 2020 that there was a shortage of 250,000 data scientists across industries in North America alone. For manufacturers, who aren’t always located in technology hubs, the challenge is even more acute.

“For many manufacturers, venturing into data science as a capability is limited by two factors,” Floyd said. “Their data platform consists of many generations of legacy systems without any common method to utilize the data, and they need modern tools that can democratize data science so it can be an advantage for many roles across the organization.”
Fortunately, cloud capabilities have advanced beyond simply collecting the data, and are now able to organize and analyze it in such powerful ways that advanced work can be done without expertise in data science.
The role of data science in manufacturing
In manufacturing, data science can fall into two general categories: business intelligence and factory operations.
On the business intelligence side, data scientists do what they do in many other industries: demand forecasting, inventory management, price optimization, and predictive analysis. Data science helps companies understand what’s happening in their business and predict what’s coming next, to help make better and more informed decisions.
More specific to manufacturers, data science can help improve processes within the operation. All of those robots and other machines on the factory floor are now equipped with sensors, flooding engineers with more data than ever before. Optimizing and operationalizing this information is a monumental opportunity to help manufacturers transform their businesses.
“There's a massive amount of data that you can collect from these machines,” Sheridan said. “You can connect millions or billions of data points.”
There are many areas where data science can help improve factory operations, including:
Monitoring: Flag problems with machines to reduce downtime and waste.
Optimization: Identify optimal points in the process to increase throughput and quality.
Analysis: Help determine the root cause of failures and accelerate improvement of machines.
Supply chain management: Ensure the factory floor has all necessary raw materials without shortages or delays.
Automation and artificial intelligence: Data science is the foundation in which automation is built, such as enabling visual inspection AI for quality assurance, or optimizing and calibrating machine performance.
Predictive maintenance: Not only forecast when and how machines might fail, but also improve quality and reliability on the line.
Simulation: Digital twins can be used for visualization and to create scenarios to acquire data on the impact of potential decisions.
“It's about getting visibility into the data and actually understanding how your factories are performing from both a machine-level capability, and from an operations perspective,” Sheridan said. “We want to enable everybody, from the floor technician to various operators, to become data scientists without having a Ph.D.”
Enabling engineers to perform data science operations
F.S. Fehrer Automotive, one of the leading manufacturers for vehicle seating and interior components globally, has production lines that can produce up to 10,000 foam parts per day. And with each part generating up to 2,000 data points, Fehrer found several years ago that it was creating a cumbersome amount of data on a daily basis.
“The amount of data we can generate is so large that we had not been able to store it properly,” said Tobias Riedel, director of Fehrer’s central operational service. “It’s quite a large amount of different information that we can get out of our production lines, but we have not really able to analyze this because we have not had the data expertise, only the experience of our process engineers.”
Over the last few years, the company has invested in automated operations to improve production metrics and optimize quality. When Fehrer began its journey to organize and operationalize its data around 2010, it was starting from nothing, using spreadsheets to store machine data while working with a local university’s department of applied science in Germany.
The goal of using AI is to spread all the capabilities of the equipment and not to rely on a single person, so as to make the process more robust by relying on data.
Tobias Riedel, Director, F.S. Fehrer Automotive
The company knew it had to graduate from these outmoded systems if it was ever going to scale to meet the demands, and possibilities, of its data.
Working with Google Cloud’s Manufacturing Data Engine, along with its business intelligence platform Looker, Fehrer has taken steps towards gathering and understanding its data streams across production. The company is currently running a pilot project encompassing one of its production lines, with the goal of expanding to full global operations in the next couple of years.
“A broader range of operators”
The goal is to give its experienced process technicians the ability to easily see, understand, and analyze production data to make their jobs easier and more efficient. Essentially, the Manufacturing Data Engine pilot will give these engineers the ability to work more like data scientists.
“We were looking to find a solution to make the manufacturing process accessible to a broader range of operators,” Riedel said. “Moreover, we want to find a solution to get the real associations between the machine data and efficiency.”
In short, the pilot aims to help workers improve both real-time operational and long-term strategic decisions based on the information and guidance provided by the software accompanying their hands-on work.
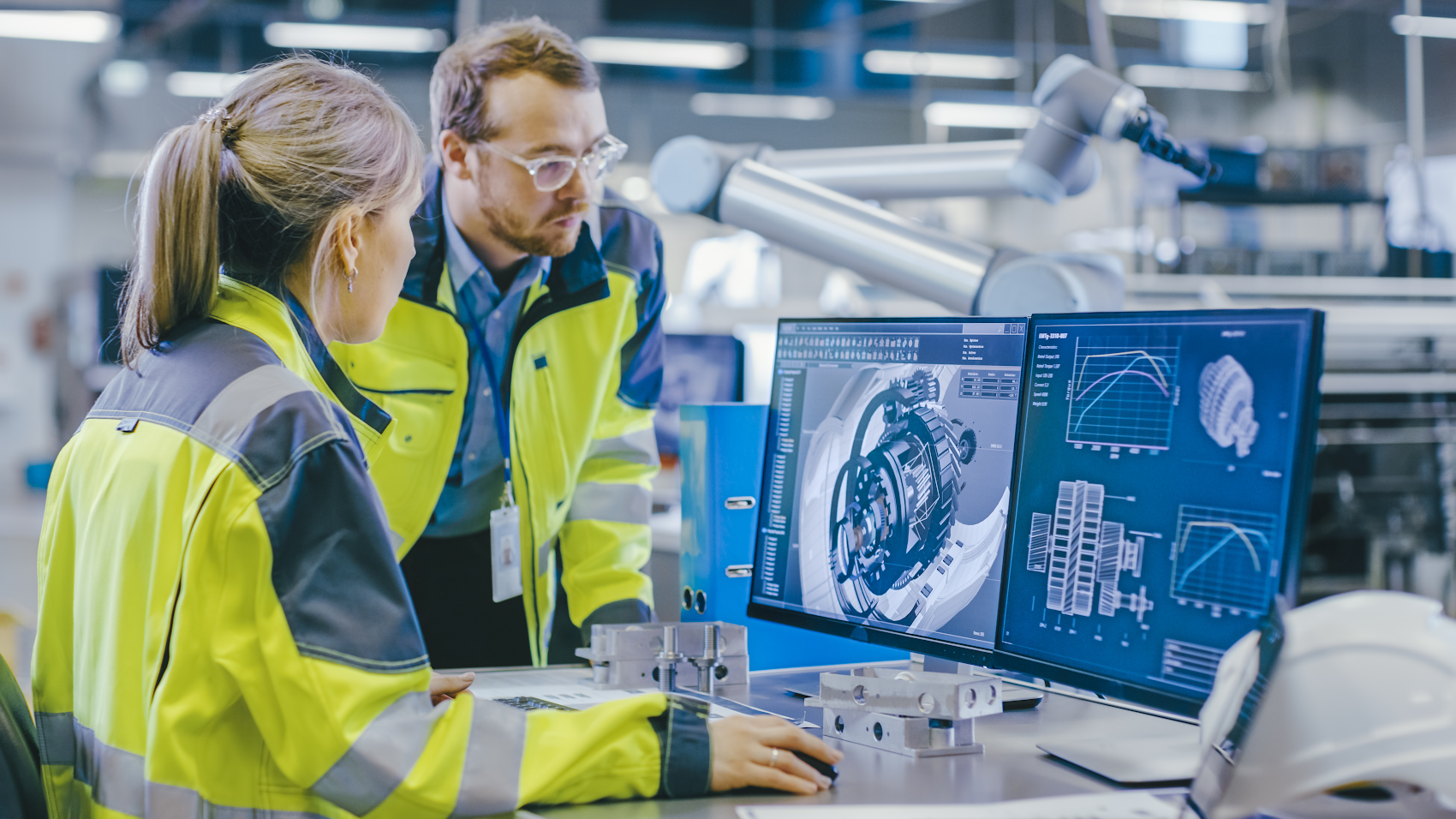
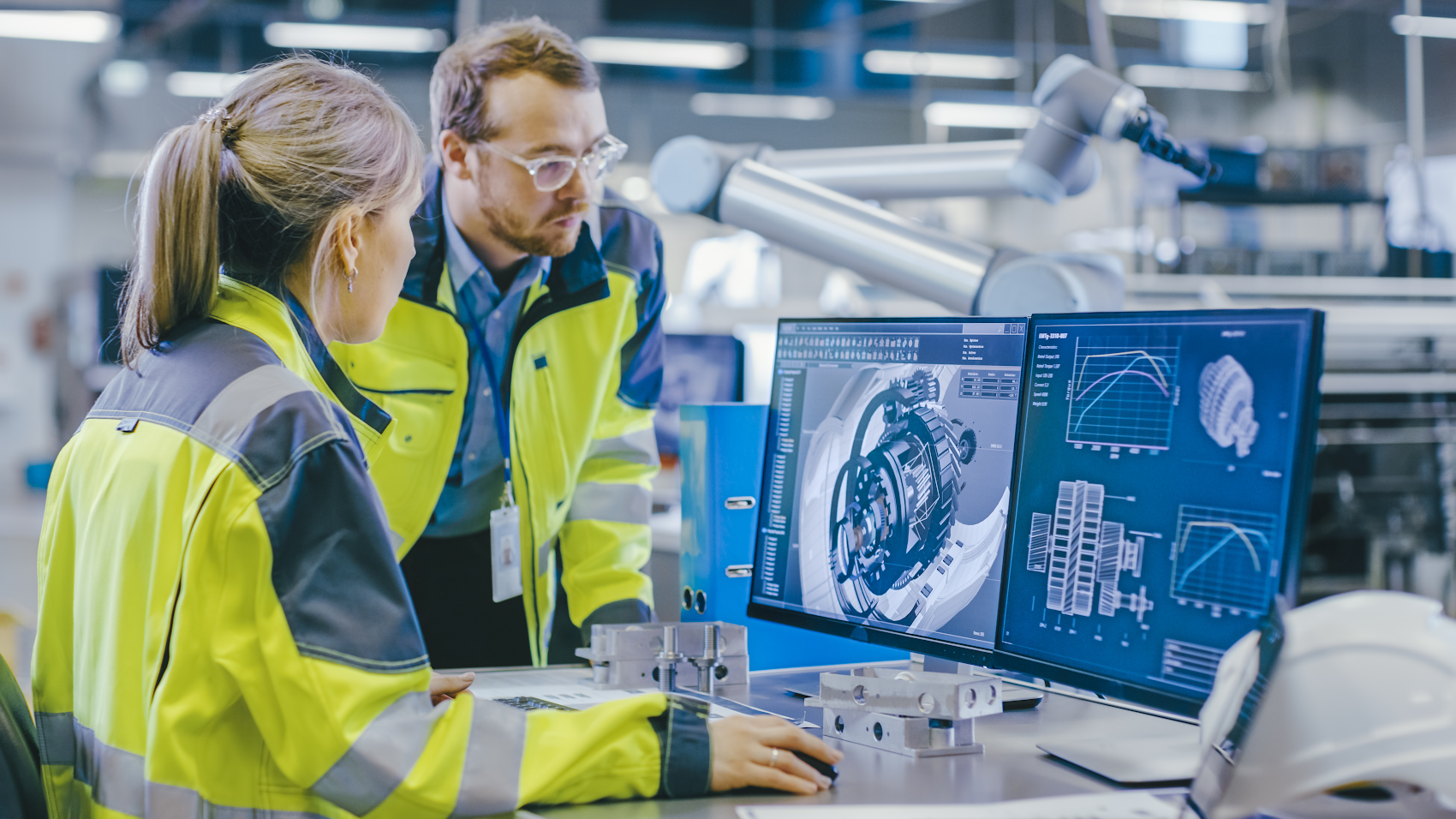
“We want to find a way to implement what we call predictive quality,” Riedel said. “We want to be able to identify when the relevant sensor values are drifting into a certain abnormal area and give the operators a warning before we produce bad parts. And maybe in the next couple of years, we can develop a functionality that, when certain sensor values are changing, the machine will change its settings automatically.”
The next step for Fehrer after maturing its data operations is to apply more analysis, automation, and artificial intelligence to improve its processes. The company has started a pilot project with Google Cloud’s Visual Inspection AI to improve the efficiency of their optical inspection. This work can create a virtuous cycle, where improved AI and operations can lead to better data collection, which enhances automation and AI, and so on.
“The goal of using Visual Inspection AI is to spread the technical know-how regarding the equipment and not to rely on a single person, so as to make the process more robust by relying on data, not on only on experiences,” Riedel said.
Integrating advanced artificial intelligence
Companies like Fehrer will find it easier to expand AI on the factory floor than they would have just a couple years ago. Recent advances in database management, AI, and machine learning have made the role of both data scientist and engineer easier. For instance, engineers do not always have to build AI/ML algorithms from scratch. Automated machine learning (AutoML) enables developers with limited machine learning expertise to train high-quality models. When data models begin to drift, machine learning operations (MLOps) can provide continuous monitoring and optimization to calibrate models in deployment.
Traditional systems often lack dynamic capabilities and rely on batch jobs for anomaly detection, resulting in slow responses to early indications of equipment issues. Google Cloud's TimeSeries Insights API is one example of a cutting-edge anomaly detection solution designed to provide ultra-low latency detection on vast amounts of high frequency streaming data. As part of the Manufacturing Data Engine, the TimeSeries Insights API allows manufacturers to transition to real-time monitoring and anomaly detection, regardless of equipment fleet size.
The possibilities for AI in the factory are just beginning to be explored by the industry at large. A solid data foundation can help manufacturers get more out of their AI initiatives.
"The data can be organized in a way that is conducive for AI-based functions such as predicting machine health or forecasting inventory," Floyd said. "There are many practical applications where we can apply artificial intelligence or advanced analytics driven by machine learning."
To learn more about how manufacturers are leveraging cloud technologies to generate value from their data, check out Google Cloud’s ebook “Data and AI: How the Cloud is helping manufacturers transform at scale.”